“The needle is such a familiar item that people may mistakenly regard it as a simple tool,” says Harada. “But the manufacturing process is both complex and sophisticated, requiring many different technical processes including cutting, stamping, grinding and electro-plating. Hiroshima manufacturers have worked continuously to improve each process, and to create innovative needles to serve varied needs.”
Like when making a fine sword, the steel is quenched and tempered so the needle will be strong and flexible yet resistant to bending and breaking. The eye is polished inside and out for easier threading, and the point undergoes a high-density abrasive polishing treatment to ensure sharpness.
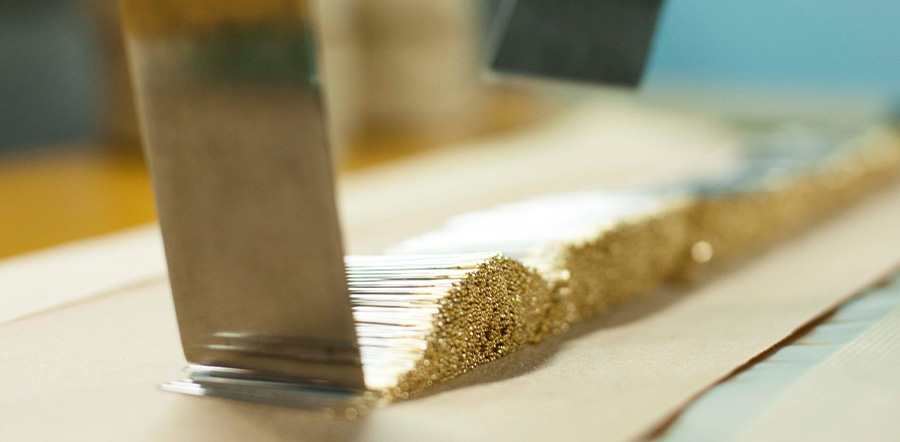
These needles need to be strong and flexible, yet resistant to bends and breaks
Even when a needle breaks or its tip becomes dull, it isn’t simply discarded. By long tradition, needles and pins that have outlived their usefulness are taken to temples or shrines. To ensure a “soft landing” on their way to retirement, the tiny tools are placed point-down into a smooth cake of tofu. Then, in a ritual called hari kuyō, they are thanked for their service. The custom began some four hundred years and is still observed at certain temples and shrines around the country, usually on the 8th of February or December.
“A quality needle is much more comfortable, allowing you to sew for hours without fatigue,” says Mutsuko Yawatagaki, a professional quilter and needlework instructor. “You get better results, too. Good tools make for good work.”